---title: "Materials and Safety"---# Chapter 3: Choosing the Right Plastics## Food Safety FirstWhen 3D printing anything that contacts food or beverages, material selection is critical. Not all filaments are created equal.## Primary Material: PCTGAfter extensive research and testing, PCTG (Polyethylene Terephthalate Glycol-Modified) emerged as the ideal choice:### Why PCTG?- **Chemical resistance** to coffee acids- **Temperature stability** up to 80°C+- **FDA approved** formulations available- **Clear printing** for visual inspection- **Low moisture absorption**### PCTG Specifications```Glass transition: 80°CPrint temperature: 245-260°CBed temperature: 70-80°CChemical formula: (C10H8O4)n```## Gasket Material: TPE/TPUThe NoDrip XL uses an optional TPE disc gasket for improved sealing:### Options Tested1. **TPU 95A** - Good flexibility, difficult adhesion2. **TPE 85A** - Excellent seal, tricky to print3. **Silicone** - Ideal properties, requires casting### Final Choice: TPE Disc Gasket- Designed as a separate disc for easy replacement- Shore hardness ideal for sealing- No-drip performance when properly installed- Food-safe formulations available- Optional component (cap works without it)## Materials to Avoid### Never Use- **ABS** - Releases harmful fumes, not food-safe- **Standard PLA** - Degrades with heat and moisture- **Nylon** - Absorbs water, affects coffee taste### Use with Caution- **PETG** - Similar to PCTG but less chemical resistant- **PP** - Difficult to print, may warp- **PC** - Requires very high temperatures## Surface Finish Matters### Layer Adhesion- Proper temperatures ensure no gaps- Avoid under-extrusion at all costs- Consider 110% flow rate for solid walls### Post-Processing1. **Sanding** - Removes layer lines2. **Vapor smoothing** - Not recommended for PCTG3. **Food-safe coating** - Optional but adds complexity## Testing for Safety### Visual Inspection- Check for gaps between layers- Ensure no stringing or blobs- Verify smooth internal surfaces### Water Testing1. Submerge in hot water (90°C) for 10 minutes2. Check for deformation or degradation3. Inspect for any discoloration### Practical Testing- Brew with water only first- Check for any off-tastes- Monitor for degradation over time## Sourcing Materials### Recommended Brands- **Prusament PCTG** - Consistent quality- **FilamentOne PCTG** - Good clarity- **NinjaTek Chinchilla** - Excellent TPE### What to Look For- FDA compliance statements- MSDS availability- Consistent diameter (±0.02mm)- Proper storage (sealed, dry)## Storage and Handling### Filament Storage- Sealed containers with desiccant- Print directly from dry box if possible- PCTG: <20% humidity ideal### Printed Parts- Wash with dish soap before first use- Store dry between uses- Replace if any degradation appears## The Microplastics QuestionThis deserves its own chapter — see Chapter 6 for a detailed discussion of microplastic concerns and mitigation strategies.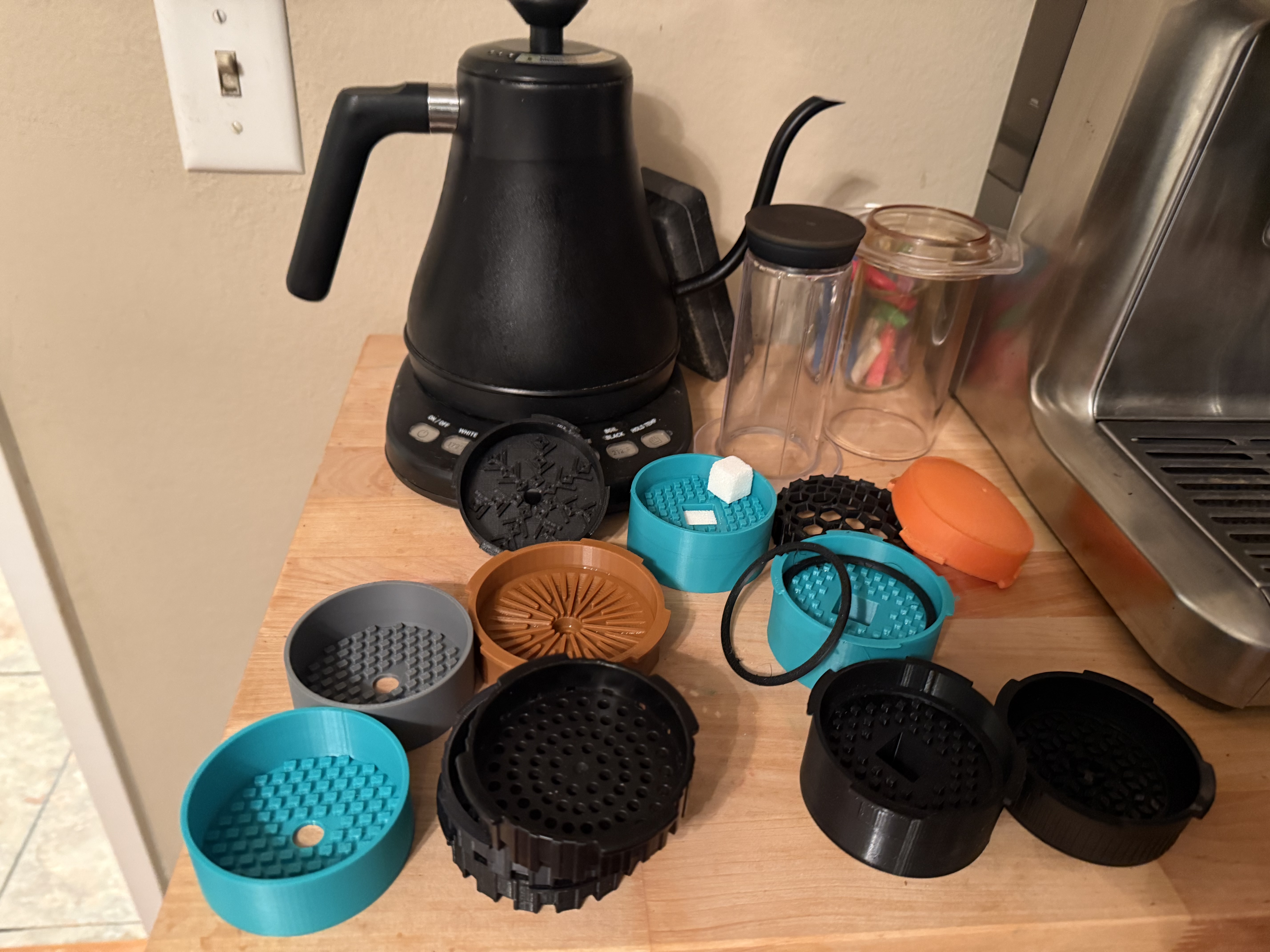## Key Takeaways1. **PCTG** is the optimal choice for the main body2. **TPE** provides excellent gasket properties3. **Surface quality** matters as much as material4. **Regular inspection** ensures continued safetyNext, we'll dive into the actual printing process and settings that make it all work.